Click the simple table below to view the FULL LENGTH Mechatronics Course for Teen OVERVIEW
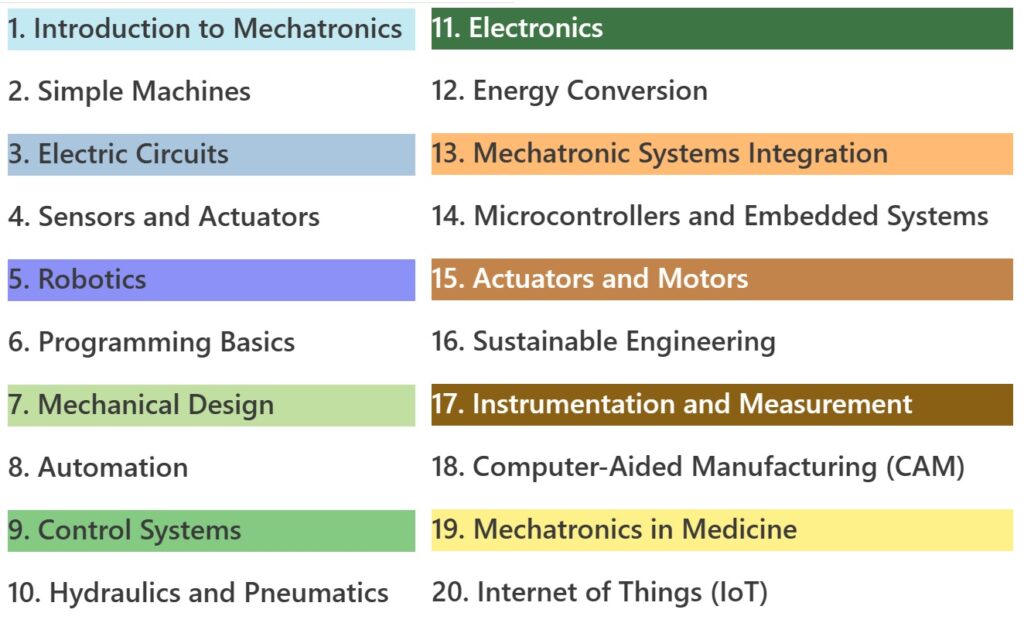
DISCLAIMER – This course is put together from various sources. Although the content of the course, and the questions are written and designed by Total Electrical Training, however none of the video tutorials in this course are made by us, or anyone affiliated with us. Although we’ve compiled the videos to enhance your learning of the relevant lesson, this does not mean Total Electrical Training is validating or promoting the creators of those videos or the content of their channels.
This Lessons Contains: READING, VIDEOS, and QUESTIONS
Understanding Control Systems in Mechatronics
What is a Control System?
A control system is a set of devices or algorithms designed to regulate the behavior of other devices or systems. It aims to achieve a desired output or performance by manipulating the inputs to the system based on a set of predefined rules. Control systems are ubiquitous in various applications, ranging from simple household appliances like thermostats to complex industrial machinery and robotics. At its core, a control system monitors and adjusts the system’s performance to ensure it operates as intended.
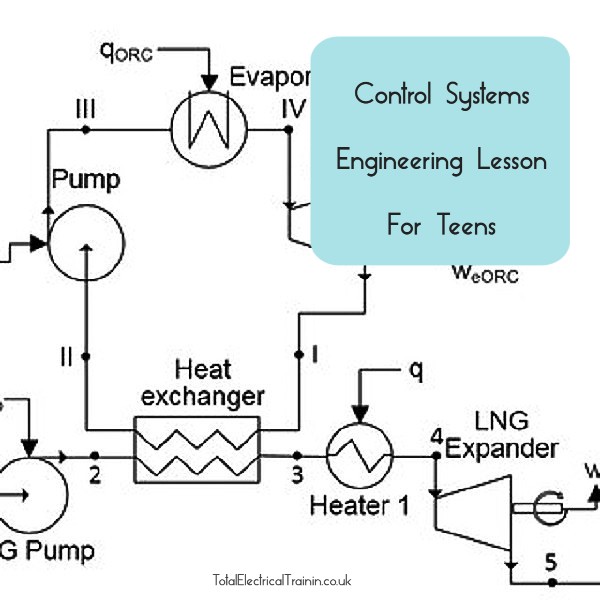
Feedback and Feedforward Control: A Comparative Overview
Feedback Control
Feedback control is a dynamic system that adjusts its operation based on the output it produces. It works by continuously measuring the output of a process and comparing it to the desired setpoint. If there is a deviation between the actual output and the desired output, the system generates an error signal. This error signal is then used to adjust the input to the system in a way that minimizes the error.
For example, in a home heating system, the thermostat measures the room temperature (output) and compares it to the desired temperature (setpoint). If the room is too cold, the heating system is activated to raise the temperature.
Feedforward Control
Feedforward control, on the other hand, attempts to anticipate changes and make adjustments before the output is affected. This type of control uses a model of the process to predict the effects of disturbances and make proactive changes to the inputs. Unlike feedback control, feedforward control does not rely on error correction after a disturbance has affected the system but rather aims to prevent the disturbance from impacting the system in the first place.
For instance, in a chemical mixing process, if the temperature of one of the inputs changes, a feedforward controller might adjust the mixing speed or the amount of another ingredient to maintain the desired output quality.
What is PID Control?
Proportional-Integral-Derivative (PID) control is one of the most widely used control algorithms in industrial and commercial applications due to its simplicity and effectiveness. It combines three distinct control strategies to regulate a system:
- Proportional (P) Control: This part of the controller responds proportionally to the current error. If the error is large, the proportional response will be large, and vice versa. However, proportional control alone cannot eliminate the error entirely and might lead to steady-state error.
- Integral (I) Control: This component sums up past errors over time, effectively integrating the error. The integral action increases the system’s response to eliminate steady-state error, ensuring that the system eventually reaches the desired setpoint.
- Derivative (D) Control: This part predicts future errors based on the rate of change of the error. By considering the error’s rate of change, derivative control can improve the system’s stability and responsiveness, particularly in the presence of rapid disturbances.
The combination of these three actions allows the PID controller to provide a balanced and responsive control strategy that can handle a variety of dynamic conditions.
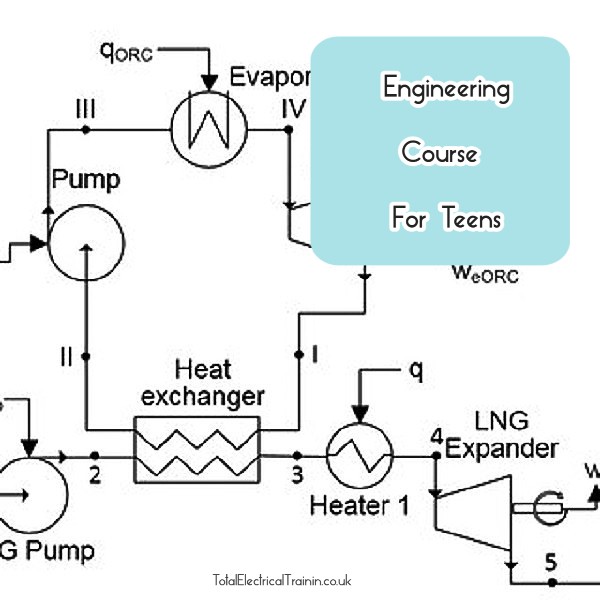
Importance of Control Systems in Mechatronics
Mechatronics is a multidisciplinary field that combines mechanical engineering, electronics, computer science, and control engineering to design and create intelligent systems and products. Control systems are crucial in mechatronics for several reasons:
- Precision and Accuracy: Control systems enable precise regulation of mechanical and electronic components, ensuring that mechatronic systems perform their tasks with high accuracy. This is essential in applications such as robotics, where precise movement and positioning are critical.
- Automation and Efficiency: By automating control processes, mechatronic systems can operate efficiently with minimal human intervention. This leads to increased productivity and reduced operational costs.
- Adaptability and Flexibility: Advanced control systems can adapt to changing conditions and disturbances, allowing mechatronic systems to maintain optimal performance even in dynamic environments. This is particularly important in industries like manufacturing, where conditions can vary frequently.
- Safety and Reliability: Control systems enhance the safety and reliability of mechatronic devices by continuously monitoring performance and making real-time adjustments. This is vital in applications such as automotive safety systems and medical devices, where failure is not an option.
In conclusion, control systems are the backbone of modern mechatronics, enabling the development of intelligent, efficient, and reliable systems. By understanding and implementing feedback, feedforward, and PID control strategies, engineers can create sophisticated mechatronic solutions that meet the demands of today’s technological landscape.
There is NO Hands on Project for this Lesson
Questions
- What is a control system?
- How do feedback and feedforward control differ?
- What is PID control?
- Why are control systems important in mechatronics?
- Bonus: Research the use of control systems in space exploration.
Ready to take a dive into Electrical Engineering to get a head start on College or University, or simply expand your DIY knowledge?
Check out our meticulously designed course in Electrical/Electronic Engineering for all walks of life, from any country. Delivered by Professor F. Tavassoli.
Buy me a Coffee
I would be honoured if you’d buy me a digital coffee to express your thanks for this Mechatronics Course I’ve put together to help eager minds excel in their knowledge, learning and success.
Your kind donation makes it possible for me to continue creating amazing content and fulfil my dream of keeping the majority of what I make FREE and Ad FREE!!!
Thank you from the bottom of my heart, and abundant blessings to you!
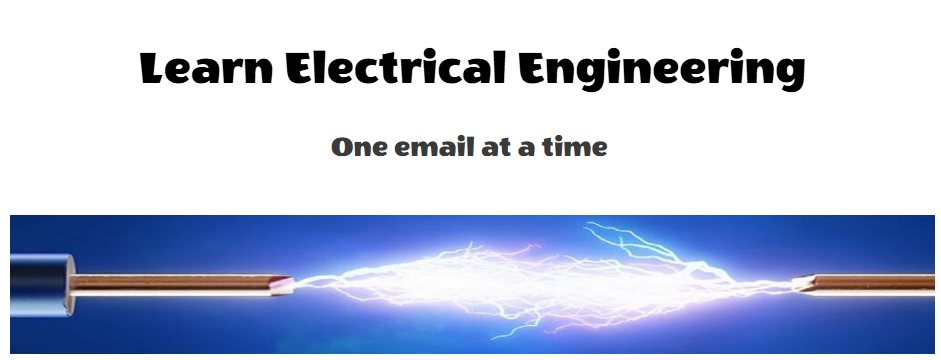
Join students and professionals
from across the world increasing their knowledge of Electrical Engineering.
One email at a time
We never send spam or give your information to anyone, Privacy Policy here.
DISCLAIMER – This course is put together from various sources. Although the content of the course, and the questions are written and designed by Total Electrical Training, however none of the video tutorials in this course are made by us, or anyone affiliated with us. Although we’ve compiled the videos to enhance your learning of the relevant lesson, this does not mean Total Electrical Training is validating or promoting the creators of those videos or the content of their channels.